This is the last piece that will
finish the tank. It's a sump which is the low point of the tank and the
gas lines will hook into it. Now it's time to drill two holes and then
weld some fittings to it.
|
|
I'm going to use # 8 AN fittings to
run my fuel lines like the tank has. These fittings are made by
Earl's and are made out
of steel. They will be a challenge to weld because of the thickness
difference between the two.
|
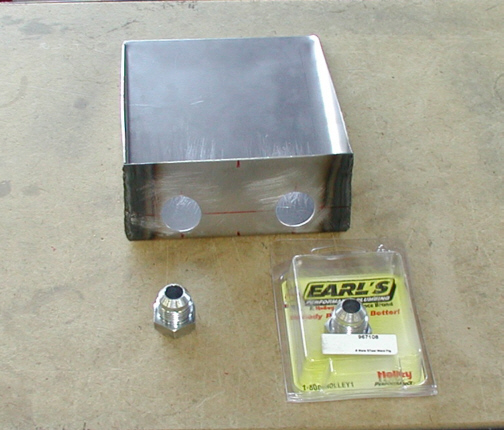
|
This is where the sump will get welded
on to the bottom of the tank. I cut this opening with my Dremel and made it 2" smaller in
both directions so I would have plenty of material to weld too. Once the
sump is welded on, the fittings will stick out past the front edge of
the tank for easy hookup of the fuel lines. Now would be a good time to
tighten the rollover vent valve. |
|
Now that the sump has been welded on,
it's time to weld on four hold-down brackets. One thing that happened
while I was in the middle of welding the sump on was that the tank made
a loud noise and scared me. I guess the metal stretched and moved while
it was hot to the point of buckling and sounded like a bass drum which
made me jump. After my nerves had settled down, I continued welding and
it happened a second time. Now I was gun shy and decided to let the tank
cool for a few
minutes and while it was cooling, it happened a third time but not as
loud as the first. Once it cooled down completely, the bottom was much
straighter than before. I started welding again and finished without it
making me jump again. I've never had that happen to me before but
then again, I've never welded something this big out of something this
thin either.
|
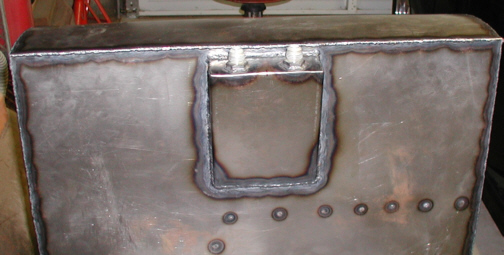
|
1 2
3 4
5 6
7 8
9 10
11 12
13 14 15
16 17
18 19
20 21 22 23
24 25
26 27
28 |
29
30
31 32
33 34
35 36
37 38 39 40
41 42
43 44
45 46
47 48
49 50
51 52 53 |
54
55
56 57
58 59
60 61
62 63
64 65
66 67
68 |