Working With Plastic Continued
Now that my lathe is working again, it's time to turn those squares
into some round pieces. I made the diameter .735" to .740", which is
just under 3/4".
|
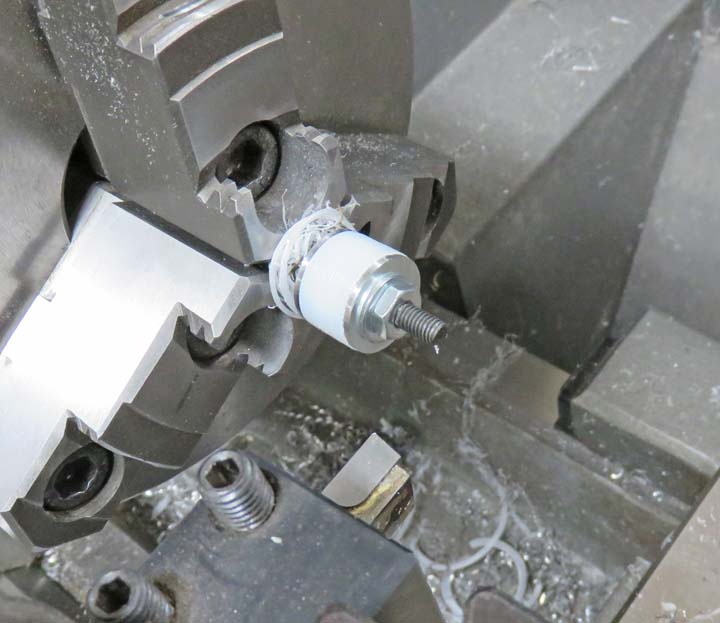 |
Here is what they look like all finished.
Now it's time to work on some aluminum again.
|
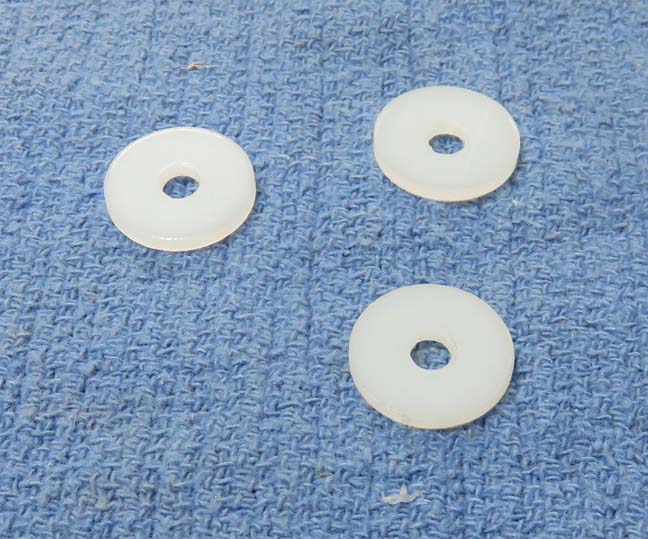 |
Working With Aluminum Again The depth of the pockets are .056" to .057". This way
the plastic stays proud by a few thousands. If you're wondering why
there are two different diameter pockets it's because I'm using an end mill
here. Let me explain: end
mills are ground so that only the outside edges cut while it's
traversing. To achieve this, the bottom of the end mill is ground at a
two or three degree angle.
This means if
you cut or plunge straight down (like I did below), the center won't be
as deep as the outer edge (leaving a high spot in the center). To get around this I used
a second smaller end mill, (in this case a 5/8" diameter one) to achieve a
much flatter area for the plastic to rest on. It's not a perfect
solution, but it's good enough for the plastic washer to sit flat enough
to work correctly.
|
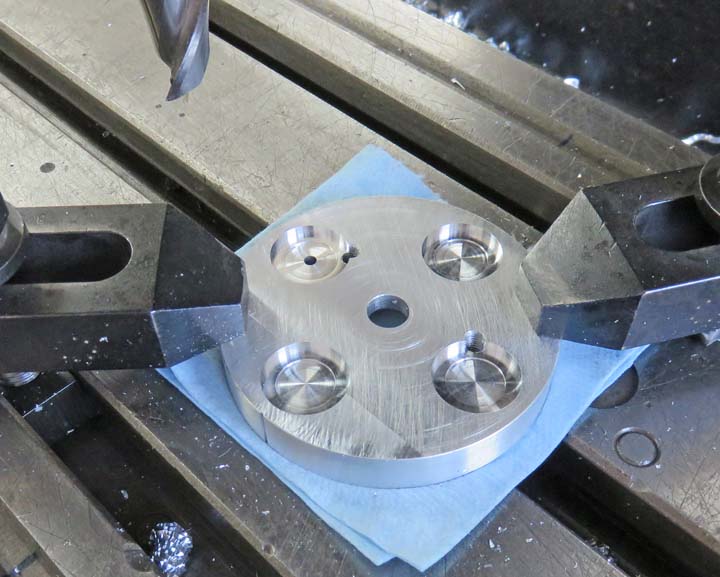 |
I purposely centered one of the pockets around the 3/16" pin. This way
the washer
will ride on the slot instead of trying to go across
it when the aluminum piece is turned.
|
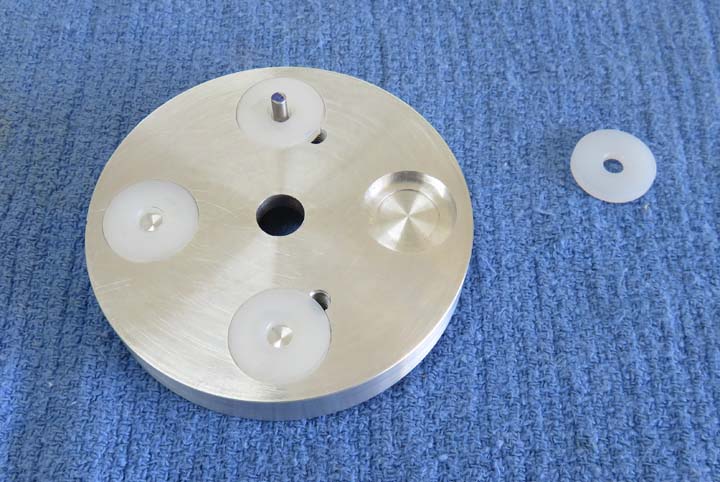 |
This is the 8 1/2" base which has the same concept as the smaller piece.
When the two pieces are fastened together, it feels like it's riding on
bearings, which is exactly what I wanted.
|
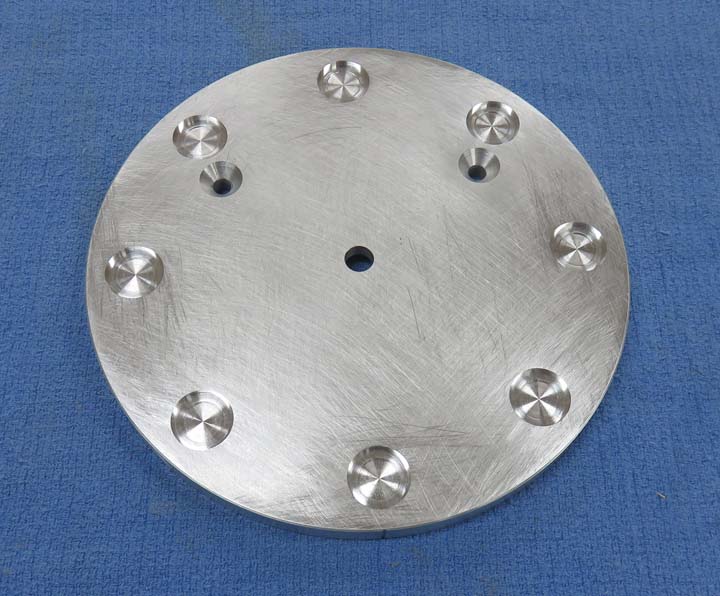 |
It's Finished
Here it is all finished.
|
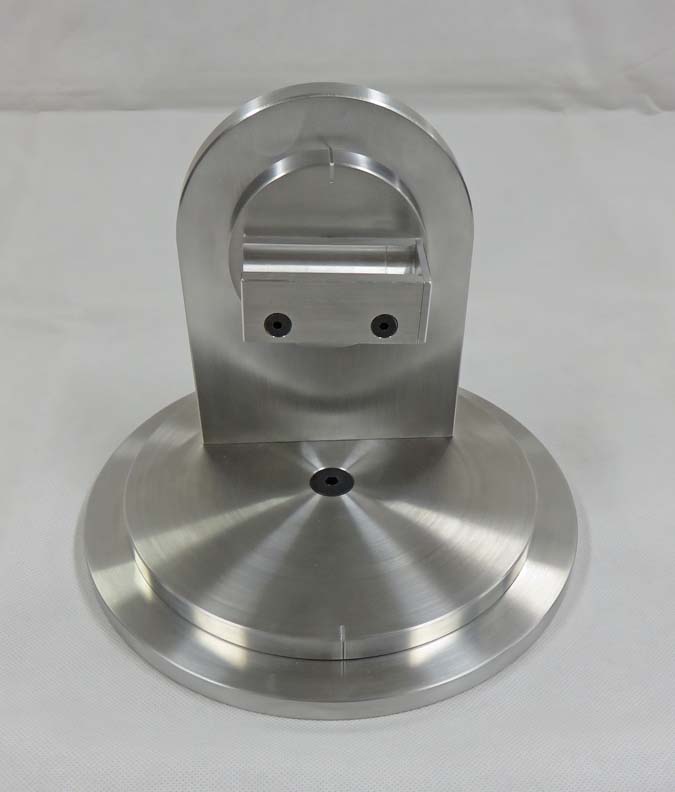 |
There will be some vinyl stickers added to the areas near the lines I
machined in.
|
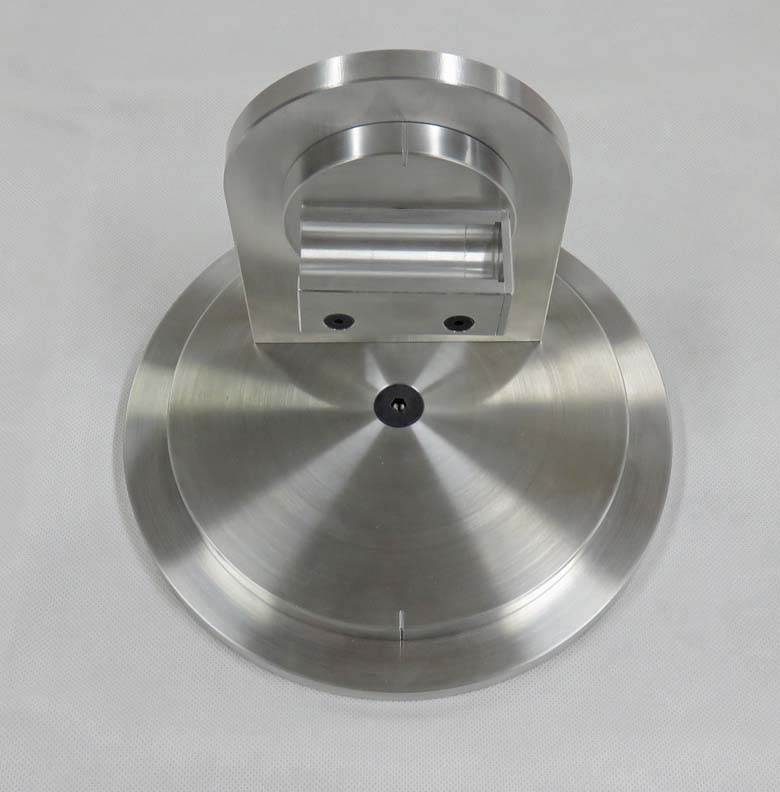 |
The base is 8 1/2" diameter and the other one is 7".
|
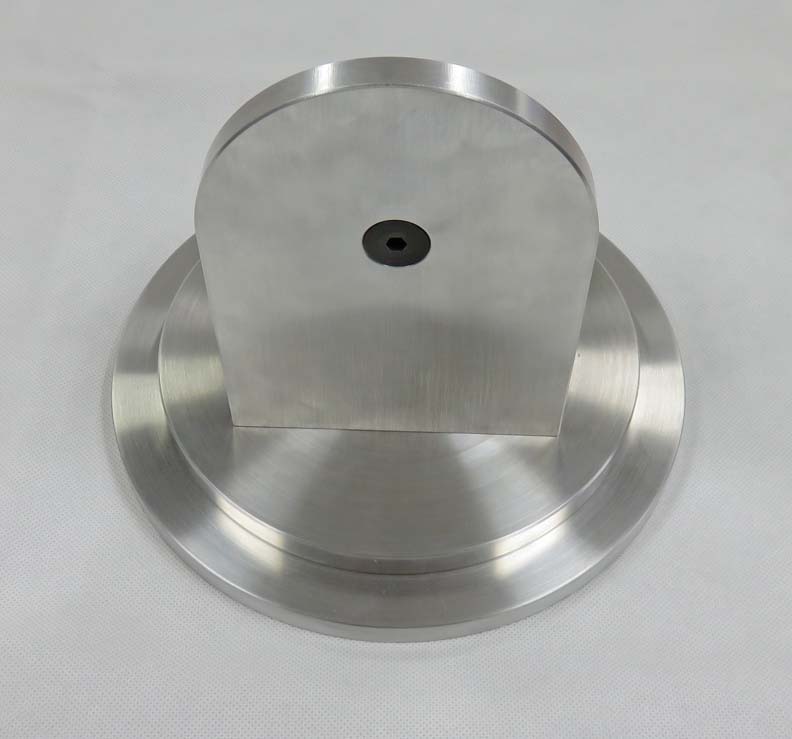 |
Here you can see a bunch of chamfers so nobody gets hurt.
|
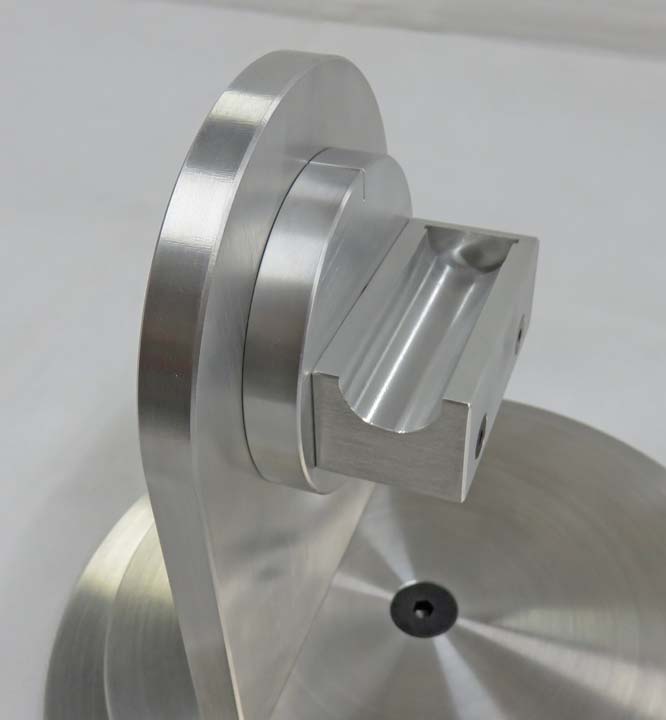 |
Plus the chamfers make it look nice.
|
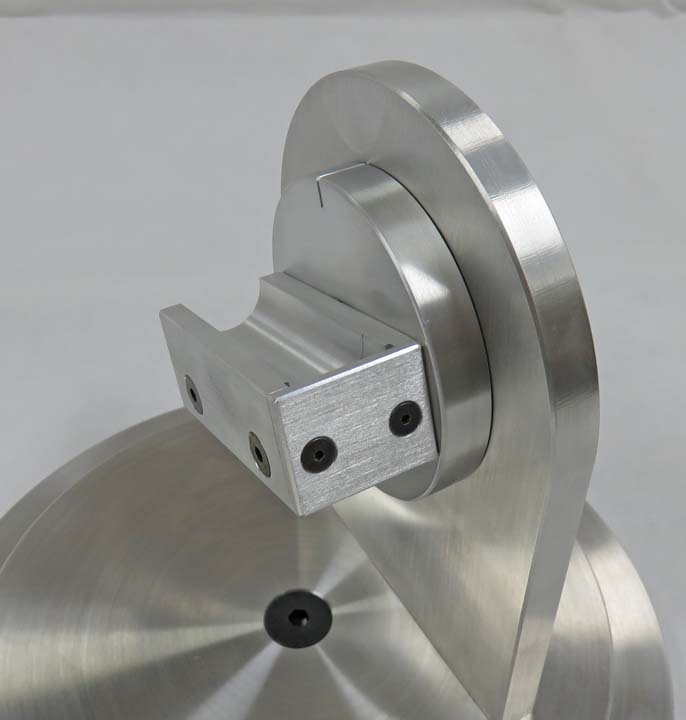 |
1
2
3
4
5
6 |